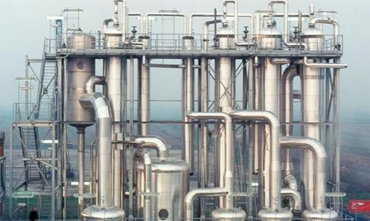
When the climatic conditions are not suitable (high humidity, low temperature) or it is necessary to reach the solution's saturation, the only possible solution is the traditional evaporation system, such as the Multiply Effect Evaporator (MEE), also if the management costs (€/m3 of water evaporated) are 4 - 6 times higher than forced air evaporators.
In the case of MEE, the evaporation of a solution is carried out by boiling in some evaporator units with gradually decreasing pressures and connected each other, so that the steam developed in one of them is the heating fluid of the next unit. The circulation of liquids from one unit to another one can take place in the same direction of the circulation of steam (co-current) or in opposite directions (counter current). The choice of feeding method depends on several factors: in case of evaporation in co-current, the maximum concentration of the solution is reached in correspondence of the lower temperature (and this is advantageous in case of heat-sensitive solutes). Instead, if we work in countercurrent, the maximum concentration is obtained at higher temperatures (and this allows limiting the increase of viscosity of the concentrated solution, benefiting the heat transfer. The optimal number of evaporators in series (effects, n) to be used in a plant of this type results from an economic balance between the cost due to consumption of energy (which decreases if n increases) and the investment cost (which increases if n increases).
Compared to the air forced evaporators, the MEE allows recovering part of the evaporated water by condensation and obtaining a saturated solution (mother liquor), easily crystallizable through next steps of cooling and heating, in order to form a solid composed of atoms neatly disposed.
To accelerate and manage the formation of salt's crystals contained in the mother water, one of the most efficient system is the Chiller. This technology, if used correctly, allows the recovery of sodium sulphate (Glauber Salt) for subsequent uses in the phases of dyeing. Given the high cost of Na2SO4, its recycling can cover up to 90% of management costs of MEE.
This technology is used as an integral part of the treatment process in a Zero Liquid Discharge Plant.