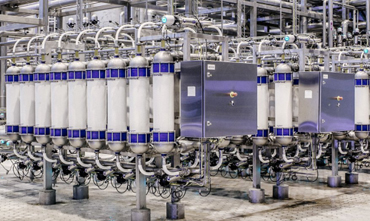
Ultrafiltration (UF) is a filtration process that operates on half-permeable membranes, characterized by pores having a diameter of 0,03 – 0,04 microns, removing particles and microbial contaminants, but releasing ions and molecules with lower dimensions. The operation's principle of the treatment is represented by the pressure difference (called transmembrane pressure, TMP), applied upstream and downstream of the filter medium, to obtain the passage of the liquid. Generally this system works with feeding pressures from 0,3 to 3 bar.
The water to be treated is pushed inside of the UF modules, obtaining a filtrate or permeate (the liquid that passes through the membrane) and a retentate which consists into suspended solids that are retained, all or in part, on the membrane surface. To restore the filtration capacity of the modules, cleaning cycles have to be performed, which include flushing in the same direction, the backwash, air cleaning, flushing with addition of chemical reagents and chemical washing. Fluxing in co-current and backwashing can remove the layer of dirt on the surface of the membrane, while cleaning with air mixed to water separates more effectively pollutants. Flushing with addition of reagents and chemical washing use chemicals to remove colloids, microorganisms, inorganic salts that clog the membrane UF internally.
There are two operating systems: Dead-end filtration (a dead end) and cross-flow (tangential flow). In dead-end filtration all the feeding water becomes permeate. In cross-flow filtration, part of the feed water becomes permeated, while the other becomes concentrated with impurities. The dead-end filtration requires less energy and has a lower working pressure than the cross-flow mode, and then reduces management costs. In contrast, the cross-flow mode allows treating water with higher concentration of suspended solids.
The ultrafiltration with membrane is already for some years a convenient and reliable technology for the treatment of purifying-sterilization of surface water and as tertiary treatment for civil and industrial wastewater. Indeed, it may substitute the treatments of clary-flocculation, filtration or disinfection, allowing to achieve significant energy savings. These systems are fully automated and have low requirements of operational labor. However, they may require frequent cleaning.
The advantages that this system can lead are:
- Elasticity of operation even in case of presence of peaks of turbidity and suspended solids
- Quick change of the membranes due to the high modularity
- Compactness of the solution
- Sterility of water produced without the use of disinfectants.
Applications
- Treatment and/or pre-treatment of surface water, sterilization
- Pre-treatment, sterilization of seawaters
- Depuration of civil wastewater
- Purification of industrial waste water
- Refinement of effluent for reuse in irrigation
- Pre-treatment for osmosis
This technology is used as an integral part of the treatment process in a Partial Recovery Plant, a Zero Liquid Discharge Plant, a Primary Water Plant or a Drinking water Plant.