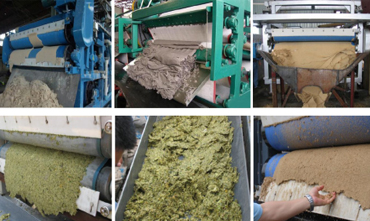
Dehydration is a physical treatment, used for the reduction of the water content of the sludge in order to:
- Reduce the volume of sludge to be disposed, with savings transport and disposal costs
- Facilitate the handling of sludge
- Remove the water excess, thus increasing the calorific value of the sludge upstream of incineration
- Adjust the water content before composting, thus reducing the use of structuring agents and soil improvers
- Reduce the emission of smells and the putrescence of sludge.
There are several technological solutions to reduce the moisture of the sludge and the identification of the most appropriate equipment is effected according to the type of sludge, the characteristics of the dehydrated products and the availability of spaces. Among the mechanical equipment, that accelerate the dehydration of the sludge, the most commonly used are Belt Presses, Filter Presses and Centrifuges.
Generally, a strong cation polyelectrolyte and a flocculant (iron's or aluminum salts) are dosed to prepare the sludge mechanically and facilitate its dehydration. The dosage can be performed directly in the thickening tank, or alternatively in the inlet line of the thickened sludge. The extra sludges (in excess), produced by biological, are taken from the thickening tank and sent to the dehydration system, by piston/screw pump, so as to obtain a sludge with a dry value of 18-23%. The draining water of the process is conveyed by gravity to the head to the water treatment plant, while the dehydrated sludge can be used as fertilizer for agriculture or it is aimed to the landfill.
Belt presses: the dehydration occurs by progressive compression of sludge between two filtering belts. The sludge, chemically conditioned, is discharged in the first draining zone, where the sludge loses much of the contained water by gravity, beginning the process of drainage. After the area of pre-drainage, the sludge passes through the pressing zone at low pressure, where there is the convergence of the two belts (upper and lower) with gradual increase of the exerted pressure on the sludge. Through the passage of the two canvases around perforated rollers with decreasing size, the pressure of squeezing increases up to the final dehydration. The cleaning of the belts is obtained by the ramps of washing nozzles that, by spraying water at high pressure, making the cleaning of the filtering belts.
Filterpresses: the dehydration is obtained by forcing the water to escape from the sludge by the actions at high pressure. Their operation's principle consists in the pressure passage of the liquid (maximum 15 bar), through the plates with filtering canvases, which retain the solid component forming the so-called "cake". The entire sequence of plates form the "filter pack", that is clamped at high pressure by an hydraulic closing piston activated by a motorized pump. The final cleaning of the canvases can be performed with automatic washing systems; for the collection and conveyance of the sludge cakes may be used fixed or mobile tanks, Archimedes screws or belt conveyor.
Centrifuges: the separation of the solid from the liquid phase takes place in a rotating drum having truncated conical/cylindric form; due to the applied centrifugal force, the solid phase (heavier) settles on the drum's periphery and it is continually removed by an internal conveyor.